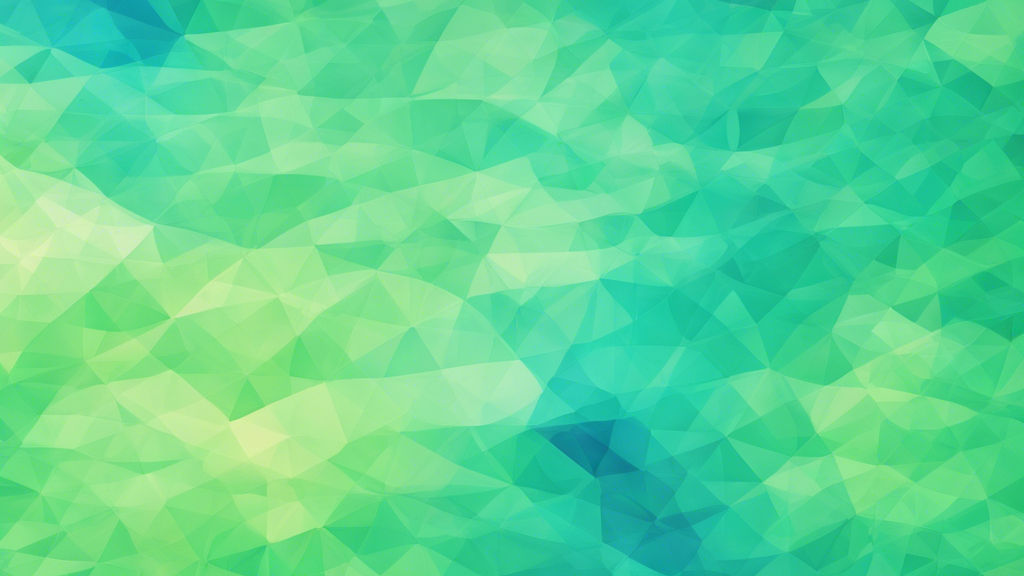
CALYX Helmet Life Cycle Analysis
As part of my life cycle analysis course, we performed a full cradle to gate life cycle analysis of the CALYX helmet. We worked with a team of senior design students as they designed this product; while they worked only on the design and user aspect, we performed comparative analyses to determine the effects the production of this helmet would have on the environment. Based on our study, we were able to additionally give recommendations to the design team in order to reduce the environmental impacts of the product.
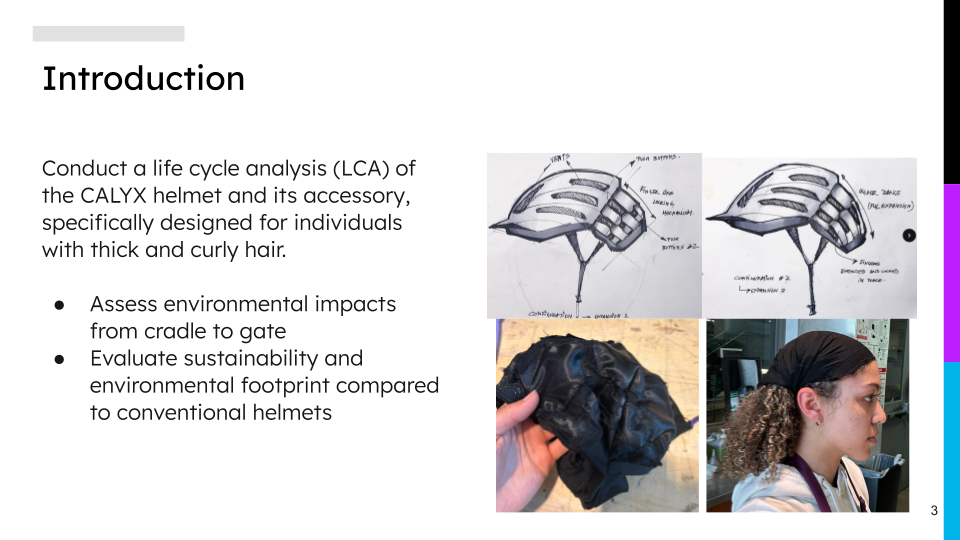
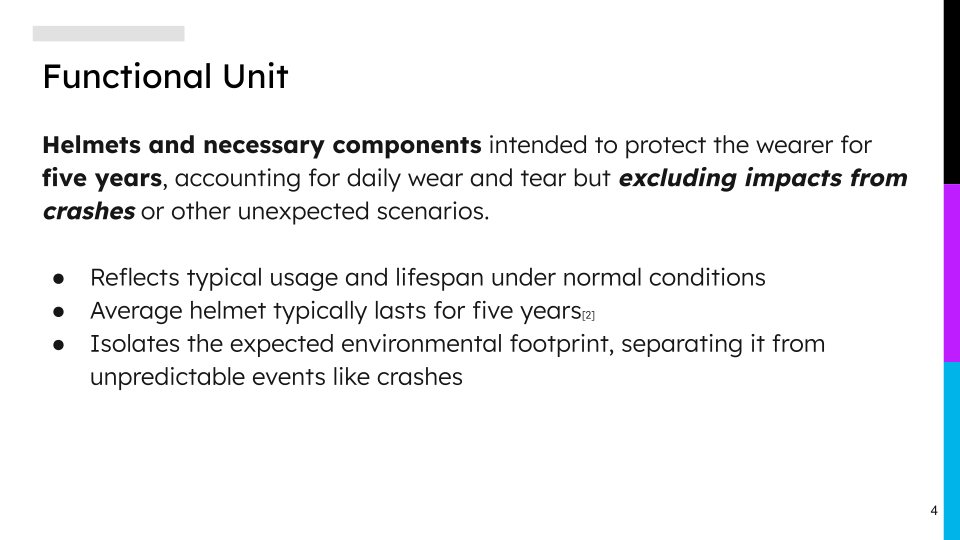
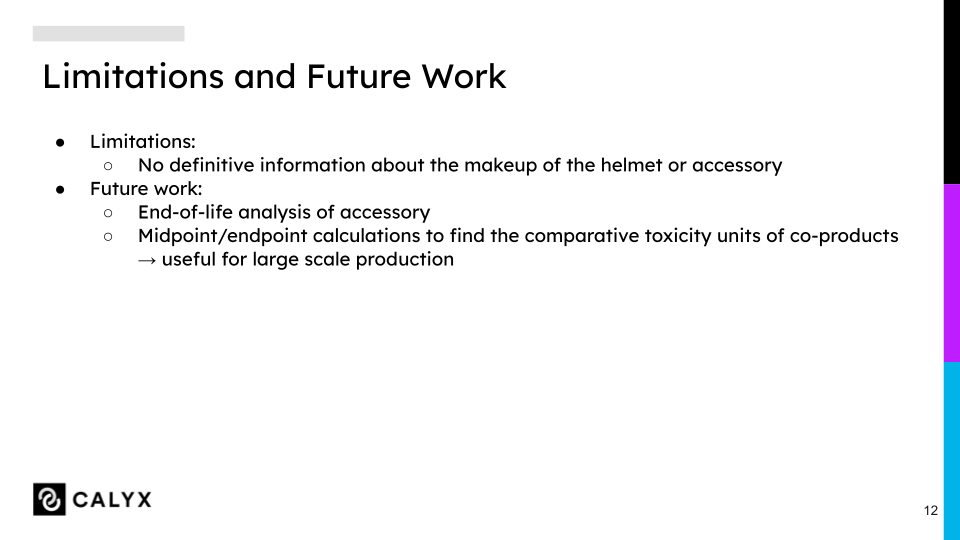
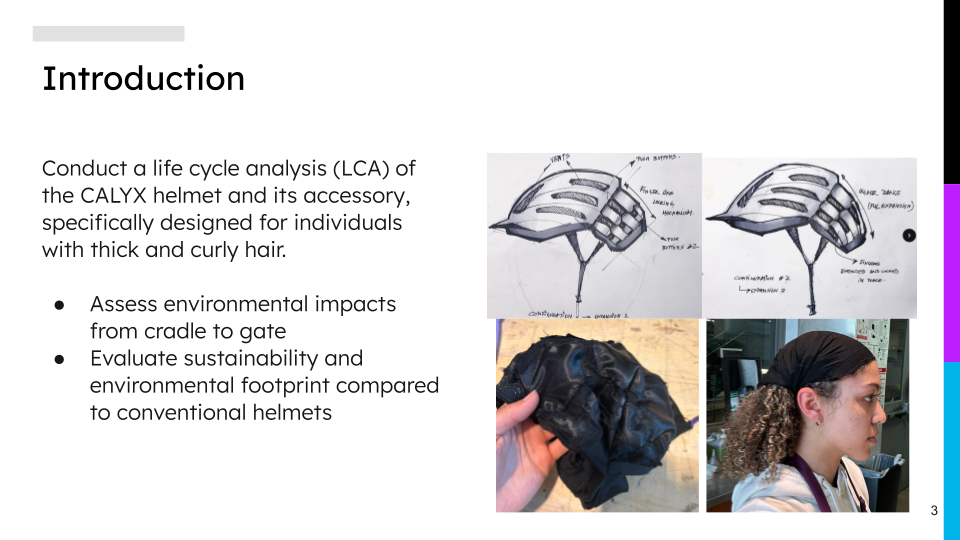
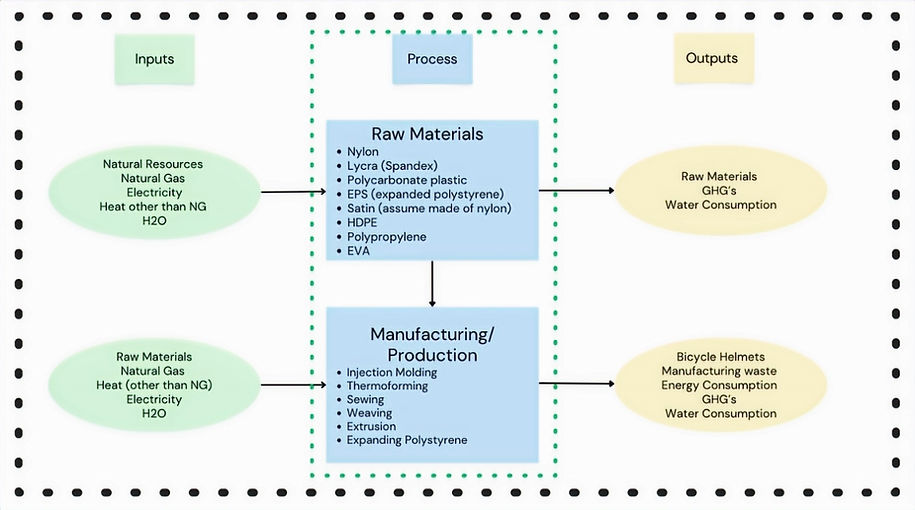
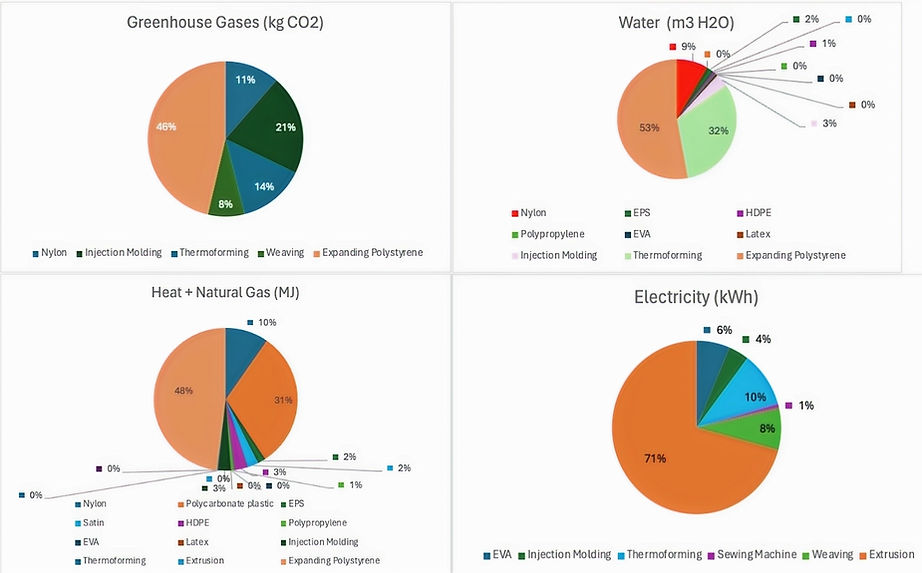
LCA Report
Introduction
Our project conducts a life cycle analysis (LCA) of the CALYX helmet and its accessory designed for individuals with thick and curly hair. This analysis addresses the environmental impact associated with the production and distribution of these safety devices, from raw material extraction (cradle) to the point they leave the production gate. This is crucial because it assesses not only the sustainability of producing such specialized helmets but also their potential environmental footprint compared to conventional helmets. Understanding these impacts is vital for developing products that are both socially inclusive and environmentally responsible, ensuring that safety advancements do not come at the cost of increased environmental degradation.
The audience for our life cycle analysis includes helmet manufacturers, environmental policy makers, and sustainability-focused consumer groups. By detailing the environmental implications of producing the specialized helmet and its accessory, our analysis aids manufacturers in identifying areas where environmental impacts can be minimized, perhaps through material substitution or process improvements. Policy makers can use the findings to support regulations and incentives that promote environmentally friendly production practices in safety equipment manufacturing. For consumers, especially those concerned with ethical consumption, our results provide clear insights into the environmental considerations of their choices in safety gear.
Life Cycle Analysis Parameters
In Life Cycle Assessment (LCA), two crucial concepts are the system boundary and the functional unit. These components are foundational to the methodology of LCA, defining the scope of the study and ensuring the comparability of results.
The functional unit serves as a critical measure within the LCA framework by providing a precise and measurable reference to which all inputs and outputs are normalized. This quantification allows for the comparison of different products or systems that fulfill the same function, ensuring that comparisons are based on equivalent services provided. The functional unit, therefore, not only clarifies what is being assessed but also anchors the entire LCA, making it possible to compare environmental impacts in a meaningful and consistent way. It captures the service performed by the product, supporting a clear, comparative analysis of options based on their performance relative to their environmental costs. This is why the functional unit is fundamental to achieving an LCA’s objectives, as it allows stakeholders to make informed decisions based on standardized data.
The system boundary defines the scope of the analysis by determining which processes and stages of a product's life cycle are included. This boundary selection is highly dependent on the specific goals of the LCA, allowing for a tailored approach that focuses on particular aspects of the product’s environmental impact. It includes only those unit processes that characterize the system, which can vary from including a comprehensive view of all life cycle stages to focusing on a particular segment such as cradle-to-gate. The definition of the system boundary must align with the LCA's goal statement, which explains the purpose and scope of the study. The system boundary thus plays a critical role in shaping the study's focus and depth, impacting the comprehensiveness and relevance of the LCA findings.
Functional Unit
The functional unit defined for our Life Cycle Assessment of the innovative helmet and its accessory is “helmets (and necessary components) utilized to protect the wearer over the course of five years, including daily wear and tear but excluding effects from crashes or unexpected scenarios.” This unit was selected because it represents the typical use and lifespan of the product under normal conditions [2].
We focus on emissions and impacts per individual helmet and accessory set to align the assessment with real-world usage patterns, enabling precise and meaningful comparisons of environmental impacts. This approach helps to isolate the regular environmental footprint of the product, distinct from extraordinary events like crashes. Furthermore, distinguishing between the helmet and accessories acknowledges the differing life cycles and usage patterns of these components—accessories may have a shorter lifespan than the helmets. This distinction is crucial for accurately measuring and managing the environmental impacts of each component separately within the broader system, facilitating a more targeted approach to sustainability improvements.
​
System Boundary and Inventory
The system boundary we chose for our life cycle analysis covers the "cradle to gate" stages, including all the processes from the extraction of raw materials to the production of the helmet, but it does not extend to the distribution, use, or end-of-life phases of the product. Seen in the diagram below all processes are surrounded by a green dashed box and the entire system boundary is enclosed by a black dashed box.
​
​
​
​
​
​​
​
​
​
​
​​​
​
For the inputs section we included natural resources and energy inputs required for the production of the helmets. It includes natural gas, electricity, other forms of heat, and water. The outputs include the finished helmets, as well as by-products of the manufacturing process like greenhouse gas emissions, manufacturing waste, energy consumption, and water usage. Quantifying these outputs is critical for assessing the environmental footprint of the manufacturing stage.The processes section details the types of raw materials used (e.g., Nylon, Lycra, Polycarbonate plastic, etc.) and the manufacturing processes involved (e.g., injection molding, thermoforming, sewing, etc.).
In our life cycle analysis (LCA), we focused on a cradle-to-gate approach, analyzing the environmental impacts from the extraction of raw materials to the manufacturing gate. This scope was chosen to simplify the analysis and accommodate the constraints of our 10-week timeline, especially considering the variability and limited accessibility of downstream data. By focusing exclusively on upstream production, we were able to concentrate on the direct impacts of raw materials and manufacturing processes, ensuring a thorough assessment within our allotted time frame.
We also decided to exclude impacts from crashes or other unexpected scenarios to standardize the analysis under typical use conditions. Including such sporadic events could skew the results, as they do not represent the standard life cycle of the product.
For the quantitative inventory of our LCA, we recorded each input in a detailed spreadsheet via datasheets primarily from ecoinvent. This includes specifying the amounts of plastics and fabrics used in kilograms per helmet, the energy consumed in kilowatt-hours of electricity, and the natural gas used in cubic meters per unit. These precise measurements are critical for evaluating the environmental burdens associated with the production of each helmet, and the detailed results of this inventory are further elaborated in the life cycle analysis section of our report.
Data Sources and Justification
The primary data source used in the analysis was ecoinvent. The geography chosen was Rest-of-World since some processes had the data for the preferred US geography, and some did not. Therefore Rest-of-World was used in order to keep these values consistent.
We chose to use ecoinvent because of the breadth of the database. Each process in the production of a helmet, excluding the sewing machine, was on ecoinvent. Additionally, ecoinvent had the necessary information on the production of raw materials. Using one source with all the necessary values was important as it maintained the highest possible level of consistency across each process.
Only the sewing machine did not have information in ecoinvent. For this, we found the wattage of an industrial sewing machine, in kWh and assumed that it took an hour for this step. Another value that was not in ecoinvent was the lower heating value of crude oil and natural gas. Crude oil and natural gas often showed up in ecoinvent as an input but in terms of their mass or volume per kg of product. In order to transform this into a heating value in terms of MJ, we had to find the lower heating value using GREET. After this step, the total heat was easily calculated. Another value we had to find was the amount of each material that went into making a helmet. These values were necessary in order to correctly find the emissions that go into one functional unit. The data from ecoinvent are summarized in Appendix A.
Co-Product handling
Co-products were not taken into consideration in this analysis. All processes used in the production of discussed helmets and accessories produced negligible coproducts, which were deemed to have no impact on production. Relevant examples include emissions such as silver (1.02e-09 kg/kg polystyrene) and nickel (5.15e-06 kg/kg polystyrene) in the production of polystyrene. While these would certainly count as co-products if produced in larger quantities, they were instead listed as emissions to air by the data sources used due to the negligible quantities produced.
Life Cycle Analysis Results
The data was compiled by examining the different raw materials and the processes that these materials went through to make the final product. Only four main categories were selected in this life cycle analysis, as they were the major components in this process compared to other key metrics: heat and natural gas, electricity, greenhouse gas emissions, and water consumption.
In conducting a life cycle analysis of a product, the selection of raw materials is a crucial component that significantly influences the environmental impact and overall sustainability of the product. When looking into the raw materials of this life cycle analysis, polycarbonate plastic plays a prominent role as it constitutes a substantial portion of the raw material inputs. This dominance can be attributed to it being the external exoskeleton that actually protects the user from impacts. This material’s unique combination of high impact resistance and durability makes it an ideal choice for applications where safety and performance are paramount. It is easy to look at the results of the life cycle analysis and conclude that polycarbonate should be removed from the system because it is a main component of the heat and natural gas metric; however, polycarbonate plastic constitutes about 80% of the functional unit.
Another major crucial consideration in this life cycle analysis is the process of expanding polystyrene. This process entails the preparation of polystyrene resin beads, which are fed to a pre-expander machine, where they are exposed to steam under pressure. Steam causes these beads to expand and soften, which are then molded into a mold cavity of the bike helmet. The mold is then subjected to further steam heat and pressure, conforming it to the shape of the mold cavity. Once the molding process is complete, this expanded polystyrene foam cools and solidifies. There is an obviously intense energy input for this process, which is why it can be seen as a major consideration in most of the key metrics. The energy intensity of the expanding polystyrene process underscores the importance of considering energy efficiency measures and sustainable energy sources in manufacturing operations.
Even though there are many different processes and steps that go into creating this bike helmet, it’s evident even from the initial data gathered from Ecoinvent that it would be an extremely intensive process from the key metrics per kilogram. Despite the energy intensity, the expanding polystyrene is an essential part of the process for producing a lightweight and impact-absorbing foam that will enhance the safety and performance of the bike helmets. An alternative option would be to look into replacing the foam with another material that’s as impact-absorbing as expanded polystyrene. This would take away the energy intensive process of expanding polystyrene; however, the hard part would be to find a material that is as effective as polystyrene while also having a process that isn’t as energy intensive. The bicycle helmet that this models is a conventional bike helmet with different proportions of raw materials to account for the additional pieces in the CALYX helmet, so the amount of polystyrene in a conventional bike helmet and the CALYX bike helmet shouldn’t differ by much. There also are not many bike helmets that do not use polystyrene as the foam impact-absorbing material, so polystyrene is probably the most reliable material.
Looking at the other components of this life cycle analysis, many of the other components are not an important contributor to the key metrics. Especially in the heat & natural gas and water metrics, a lot of the components are close to 0-1% of the makeup. This can be attributed to the miniscule amounts of some of the raw materials added, such as some of the rubber rings used to hold the excess strap that hangs off the helmet and nylon. Because some of the raw materials were scarcely used, that correlates to them not being a major component of the life cycle analysis. The processes that correspond to these raw materials also reflect their minor contribution to the overall life cycle analysis.
​
​
​
​
​
​
​
Figures 1-4: Percentages of each component of the process that constitute each key metric - greenhouse gas emission, water consumption, heat and natural gas usage, and electricity usage
Conclusions, recommendations, and areas for future analysis
Producing one functional unit cradle-to-gate requires 1.2 kWh of electricity, 92.7 MJ of heat and natural gas, 4.17 kgCO2e, and 0.17 m3 water. This result reflects one that would be very similar for a typical helmet. The only difference between the CALYX helmet and a typical helmet is the expandable mechanism that would marginally increase the total material used. However the processes and materials that are the main contributors to emissions would stay largely the same. Another difference is the accessory, which contributes only a small addition to the emissions that a typical helmet might have. Therefore, the CALYX helmet has about the same environmental impact as a typical helmet.
As described in the results section, the main contributors to the heat, natural gas, and water consumption is expanding polystyrene. This energy-intensive process is the first that would be recommended to change in order to reduce the environmental impact of this process. Instead of expanding polystyrene, an alternative could be using recycled foam or wood/cellulose foam.
Another energy intensive process included producing the polycarbonate and then thermoforming it in order to make the exterior shell of the helmet. This process is one that is necessary for the strength of the helmet as well as the aesthetics as the paint is attached to this polycarbonate layer. A possible alternative to this raw material and the method of attaching it to the helmet is bio based polycarbonate, bamboo, plexiglass, or acrylic. Even if these materials are more environmentally conscious, they might have drawbacks relating to their durability. With a material that is less durable it might need to be replaced more often or would not be considered an equivalent product.
Limitations in the study include the fact that this helmet is a novel product that is still being developed. This means that we did not have definitive information about the final weight of the product as well as the weight of each component that went into it. Variations in this can have large effects if, for example, the weight of the polycarbonate was underestimated, the emissions from the thermoforming as well as the production would be much larger. Additionally, since the accessories were not fully created, there was not the most detailed information about which materials went into it or the size. In the future, with a finished model a much more accurate assessment could be made.
Another limitation is the analysis of the co-products. Since the amounts of the co-products were small, not much thought was put into their environmental impact. More research could have been done on each of the co-products to determine if there is a material where a small amount can have a large impact. Some midpoint calculations with comparative toxicity units can be done to accurately assess the impacts of these coproducts. This can become important when thinking of large scale production of helmets where producing thousands of these helmets could produce harmful amounts of the coproducts.
In the future, it could be useful to look into the end-of-life of the material. Since we were only comparing helmets and not the accessories, we are unsure if the accessories are more damaging in the end-of-life stage. If this were the case, neglecting this stage would largely underestimate the impact of the accessory.
References
[1] Bansal, Cabrera, Iyacu, Jackson, Kaspar, “CALYX Information Document”, Apr. 3, 2024, https://drive.google.com/file/d/1BEZ5RsTJ36xbcc8zMtJtg_U5PW4YVLK3/view
[2] “How Long Do Helmets Last?” Mips, 2023, mipsprotection.com/helmet-safety/how-long-do-helmets-last/#:~:text=Bike%20helmets%20have%20a%20shelf.
[3] “The Ultimate Guide to Polyester Spandex Fabric: Benefits and Uses.” Rui Bag Factory, 2024, www.ruibagfactory.com/polyester-spandex-fabric-2/#:~:text=It%20doesn’t%20shrink%20or%20fade%2C%20and%20it,also%20known%20for%20its%20ease%20of%20care.
[4] Wang, Michael, Elgowainy, Amgad, Lee, Uisung, Bafana, Adarsh, Banerjee, Sudhanya, Benavides, Pahola T., Bobba, Pallavi, Burnham, Andrew, Cai, Hao, Gracida, Ulises, Hawkins, Troy R., Iyer, Rakesh K., Kelly, Jarod C., Kim, Taemin, Kingsbury, Kathryn, Kwon, Hoyoung, Li, Yuan, Liu, Xinyu, Lu, Zifeng, Ou, Longwen, Siddique, Nazib, Sun, Pingping, Vyawahare, Pradeep, Winjobi, Olumide, Wu, May, Xu, Hui, Yoo, Eunji, Zaimes, George G., and Zang, Guiyan. Greenhouse gases, Regulated Emissions, and Energy use in Technologies Model ® (2021 Excel). Computer Software. USDOE Office of Energy Efficiency and Renewable Energy (EERE). 11 Oct. 2021. Web. doi:10.11578/GREET-Excel-2021/dc.20210902.1.
[5] Wernet, G., Bauer, C., Steubing, B., Reinhard, J., Moreno-Ruiz, E., and Weidema, B., 2016. The ecoinvent database version 3 (part I): overview and methodology. The International Journal of Life Cycle Assessment, [online] 21(9), pp.1218–1230. <http://link.springer.com/10.1007/s11367-016-1087-8>**Note: all referenced data sheets can be found: https://drive.google.com/drive/folders/13Tr847R7rONh9t-KvwxNOSZBcP9BGPkO?usp=sharingAppendix AValues from data source, lower heating values, and mass per helmet information