
Resin Phone Case

The goal of this assignment was to 3D print a working phone case. While it was intended to be a small project, allowing students to experiment with sizing CAD with respect to pre-existing items, I wanted to make an awesome phone case I would actually use. I created a design using 507 solid bodies to emulate the layering of resin art.
Over the course of 4 iterations, I tested the sizing, resin color properties, mechanics, and protection. The final version (finished after the report was written) has working buttons, screen protection, camera protection, and shock absorption. I have been using it since.

Image 9: fit of version 2
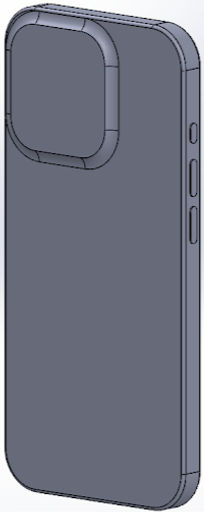

Project Report
Justin Chang Stauffer
Overview
A phone case was to be made using additive manufacturing. The design was based on a few key ideas. My requirements, in addition to the constraints imposed by the assignment, included the absence of large extruding parts along with a small body that added little or no size compared to standard phone cases. I additionally wanted a hard case which allowed no chance for the phone to slip out of the case. Visually, my idea was to emulate resin painting. This would involve creating many different layers of images, separated by layers of clear resin, which can add a physical depth to the painting.
Development
Initial modeling:
Fit Testing:
Visual Designs:
Design Iterations
Version 1:
Based on this test, the physical changes included the addition of an overhanging rim around the front, as well as the increased extrusion of the camera plateau protector. Both of these features went through multiple changes in the CAD phase before the second prototype.
Version 2:
Version 3:
However, the increased hardness did come with its own sacrifices– the haptic feedback response of the buttons was largely lost, making it difficult to feel whether the button has been pressed. However, the buttons are functional, and generally work regardless of haptic feedback– although slightly different from standard cases at first, testers agreed that there would be no real issue after a slight adjustment period.
As the sides used a full hardness material, it was clear that changes must be made to enable the phone to be inserted into the case. Firstly, slots were added to the corners; these are sometimes seen in standard case designs, with a multitude of different implementation strategies. I chose the simplest method, a simple hole with no material. These would theoretically enable the case to expand slightly, allowing the user to just barely fit the phone in between the sides as they widened. Of course, the
Visual Design:
Conclusions
Generally, 3D printing is a relatively easy method for designing, prototyping, and even creating final products, depending on desired use case and materials. The precision is often much better than handmade low fidelity mockups, and the material cost can also often be less. Additive manufacturing methods are often used for precision rather than speed, though; although it is called “rapid prototyping,” both the design and manufacturing time can be much more than the name suggests. However, there are still many benefits; the lack of need for buying multiple separate materials, the easy and secure joining of multiple features without gluing processes, and the ability to iterate with very little effort after the initial creation are all massive for the design process. It can also be noted that modeling alone, without even physically manufacturing, can often be an amazing indicator and visual representation of a product.
One issue with modeling is that it is hard to tell how materials and geometries will perform prior to manufacturing the prototype. For instance, I would have to print a whole new prototype to test two different hardness levels with only a 10% difference. Additionally, I would have no way to know if a color would not show up on the final print, since it is all displayed as desired on a model.
All in all, however, this type of rapid prototyping is a very efficient method for design. As mentioned above, although it may initially not be less time consuming than other methods of prototyping, the main benefits lie in the accuracy of the models, the ability to iterate upon versions, and the ease of production. The prints can also be scaled; although it may not usually be ideal for mass factory production, even a single machine at an office or home could be used to create hundreds of a single model, and the same machine could then be changed to manufacture a completely different product with no need for physical adjustment. As I discussed initially, it could also create individualized versions of products– a single model could easily be changed to reflect a user’s color preferences, and a whole design could simply be copied and pasted to fit onto a different model of phone. In these contexts, additive manufacturing can be not just a method for prototyping, but a legitimate ideal method of individualized production.
Appendix
The following questions were asked about the second and third iterations to potential users in order to gauge functionality:
-
Do the buttons feel natural to use?
-
Can the phone be inserted into and removed from the case easily?
-
Is it comfortable to hold? Does the case add excessive weight or size?
-
Can the phone still function in all desired contexts, such as fitting into a pocket? Is any functionality hampered?
Additionally, the following questions focused on design visuals, and were specific to the third iteration:
-
Do you like the design and look?
-
Would you change anything about it?
These questions were asked informally verbatim to friends, family, and classmates, and thus individual responses were not recorded word for word. Feedback was largely similar from person to person, and the responses are summarized below. All major differences or varying responses are also notated.
-
The secondary model had a few issues regarding the buttons. Although user feedback was largely positive, there were personal grievances with the design. Users largely reported the buttons felt normal, as the haptic feedback was decent and the material selection worked well. However, I noticed that the buttons suffered heavy wear and tear, as the junction between the soft and hard materials was easy to break. Regarding the third iteration, the buttons work much better with much less wear. However, there is almost no haptic feedback, which has proven slightly confusing with some testers. The visuals also did not come out well, although this was not a concern for any individual.
-
The second iteration was easy to insert the phone into. However, as all testers generally agreed, the material was not particularly pleasant. The material also led to easy wear and tear, and it was deemed not feasible.
-
The phone was generally comfortable to hold. While the width was slightly larger than most standard phone cases, it did not greatly affect the user. The pop-out design did not generally impact any user’s ability to hold or use the phone.
-
The phone still functioned in most standard contexts. It was, however, brought up that it would be hard to attach things to the case, such as card holders or pop-sockets. This may make it difficult for some users.
-
Responses to questions 5 and 6 will be summarized together, as they were very interrelated. Everyone who I asked (and people who I did not) did like the design. (Note– this may not be fully accurate, as people do not always admit to disliking things). Some parts which drew critique include:
-
Some of the color choices were critiqued by various people, who tended to have different ideas about what the best color scheme would be.
-
The buttons and certain visual features did not fully show clearly, as the different shore-A levels cause translucency.
-
The sides are matted in a strange pattern. This was not an intentional design choice, but rather caused by the strange generation of support which I was unable to fix.
Finally, although I did not ask about this, many people did express the desire to own or buy the case, which can definitely be taken as a positive review.
The first step of the design involved the creation of the case body. I started off by creating a CAD model of my phone (iphone 15 pro) using the developer’s diagrams (image 1).
A solid block of the desired case size was extruded, and subsequently hollowed out following the shape of the phone model (image 2). Extra care was taken regarding the camera plateau– it was modeled to follow the same geometric curve on the inside and outside of the case.
Image 1: phone model
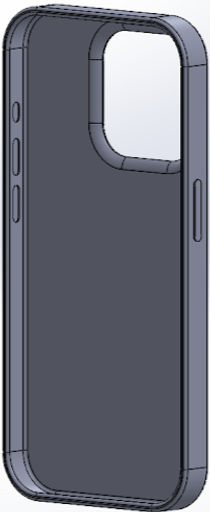
Primarily, the purpose of this step was to determine the fit of the case. It was printed on the Mk3 printer using flexible material. This step in particular highlights the largest advantages of additive manufacturing. The ability to create individual builds of high quality without any specific setup is something that is largely unique to additive manufacturing processes. If further size testing was required, or I had desired to test more features using this material, it would have been trivial to minutely modify and adjust my model and reprint within less than an hour.
Image 2: basic case shape

Image 3: initial drawing and layer scheme
Subsequent prototypes were printed on the Stratasys J826. The geometry of the part stayed largely the same from version to version, with minor changes discussed later in the design section. However, the visual modeling of this part was much more extensive. The basic idea is shown in image 3.
I knew I wanted to center it around a fox, and the design largely ended up becoming floral, even though this was not the original intention. The idea of a resin painting was maintained, and the final version ended up including 12 different layers of images, composed of around 470 solid bodies.
Image 4: final CAD with color

Truthfully, this type of work would be best done by hand. Developing an initial CAD model takes much more time than an artist simply hand painting each layer as with a typical resin painting, as each line of a drawing in cad can take a long time to fully style; multiple splines must be created to define each straight or curved line, and most splines used in this piece had between 5 and 10 different points that must each be positioned and moved separately after definition (as seen in image 5). An artist could likely paint a hollowed out phone case with this type of design in a matter of hours, where it took me over 90 hours in total to get to the point of a third iteration of print.

Image 5: spline sketch of butterfly
However, this process would become much more significant in expanding production, and especially in customization. Many people expressed desire to have this phone case design (Appendix A), and multiple people did also have different ideas for the color scheme. This would be a very feasible point that could easily be addressed with additive manufacturing. If desired, each person could create their own completely unique color scheme and print their own version of the case without any prior experience using any modeling software. This feat in particular could almost never be replicated on other types of manufacturing today.

As stated previously, this version was printed on flexible material largely for the purpose of testing sizing. Some notable features of this print included the volume button geometry; I prototyped using slits on the side of each button so as to allow the button to move independently of the rest of the case (image 8). This was removed in subsequent versions due to the fragility of the connections. The size did fit well, although the flexible material made it hard to ascertain the exactness.
Image 6: printed case version 1
Image 7: button slit


This was the first test of the J826, and also the first version for user feedback testing. This prototype was largely focused on materials tests, as the J826 has a much more extensive material catalog. Although the case was intended to be as hard as possible, there are two major reasons that flexibility is desirable; the phone must be able to easily slip into and out of the case without issues, and the volume buttons must be able to bend. As such, the sides were printed with a shore-A value of 95%, and the buttons were 70%. The back was printed with full hardness. However, these materials choices ended up creating drastic differences.
Image 8: close up of back design
The side material, for lack of a more scientific term, was gross. Even with the highest hardness level mixture, the sides were quite flexible, caving in under the slightest pressure (image 11). This, although the phone easily fit into the case and could be easily removed, caused annoyance with insertion. The sides would cave in under the force of the phone, narrowing the opening and preventing the phone from going in. Overall, the material simply provided a bad user experience in every regard, including comfort, practicality, and ease of use.

It should come as no surprise that the buttons, with a more flexible material combination, suffered the same problems. This iteration specifically used button bodies of full hardness, but the button mesh was soft. Though the buttons themselves were fine to the touch, the junctions between the mesh and the materials on either side easily began to show distress within a few minutes of testing. The case eventually split down this junction in a few days, just from minor tests.


Image 12 (below): tearing along volume buttons
Image 10 (above): bending of sides
Image 11 (left): new button geometry
Image 14: volume button design
Image 13: print of version 3

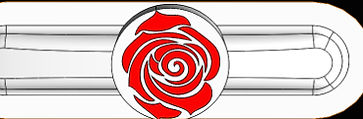
Before talking about visual design, the physical model and materials changes of version 3 will be addressed. Cavity sizing stayed the same as version 2. However, drastic changes had to be made to address the physical performance. All widths were increased from the previous version, including side length, overhang depth, and case depth. Button dimensions were changed, becoming wider as well as adding a smoother and longer transition on the inside between materials of the button and the sides (a visual element was added as well). In this iteration, the sides and back were once again printed at full hardness, and the button bodies and mesh were both printed at 95% hardness. The buttons, as users agreed, felt much better to the touch, and the case body and sides did not deform and were much more comfortable to the touch.
Image 15: slot
and overhang

existence of the overhang would provide another obstacle with the fit. To attempt to mitigate this, I separated the two millimeters of material which extended past the face of the phone, and set these sections at a shore-A level of 85%. These changes were just barely enough– the phone took about 5 minutes to carefully work into the case. However, the initial goal of creating a fully hard case was met.
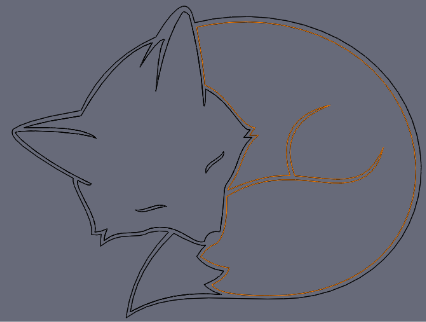

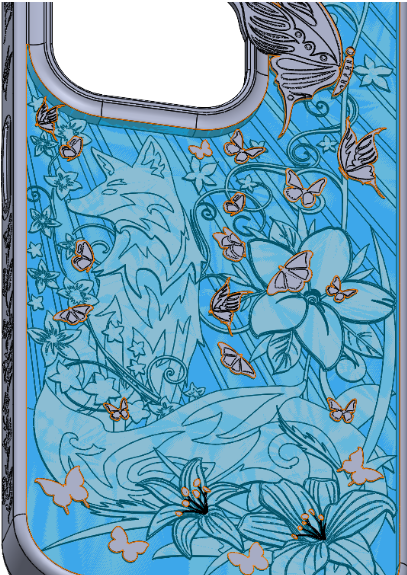
Image 16: 0.2 mm extruded design
Of course, the biggest changes between the versions were the visual designs. The reader may have noticed that the designs on versions 2 and 3 were nothing alike. Due to the lack of the ideal clear material in the J826, a quick visual test was run along with version 2. This design involved a very simple fox drawing extruded 0.2 mm, surrounded by 1 mm of clear material on each side. Although the clarity was not ideal, it was deemed serviceable and the final design idea was cleared.
The visual design of the third version was the bulk of the time and effort of this project– it alone constituted about 70 hours of design. At a basic level, drawings were created upon 12 different layers, and extruded up to differing heights. These eventually became hundreds of solid bodies, which could all be set to different colors. The remaining cavity was eventually filled with one last solid body, which could be set as the clear resin during manufacturing.
Image 17 (below): side view of layers with case removed
A few more exotic features were also added. A small border design was added to each side (images 20, 22, 24), creating another unique element almost never seen in standard phone cases. There were issues with the printing of these features, however; the sides appear to be very picky with color, as the machine simply omitted certain bodies (images 20, 22, 24). Additionally, the (unnecessary) support structure that was automatically added unfortunately overrode the desired material.
Image 18 (above): clear filling and features popped out




Images 19 & 20 (above): left side border CAD and print
Image 21 & 22 (below): right side border print and CAD
Images 23 & 24 (below): top border CAD and print


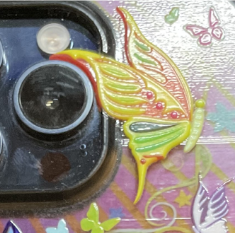


A butterfly was added overhanging the camera plateau border (image 25). This is also quite unique, and also drew the most comments during user testing.
Lastly, roses were attempted to be added to the buttons– while they marginally worked, the material and printer once again created issues, unfortunately making them almost invisible.
Image 25: butterfly overhang
Images 26 & 27 (left): button design CAD and print